Niedawno mieliśmy okazję odwiedzić fabrykę Wilk Elektronik, znajdującą się w Łaziskach Górnych, a dzisiejszy materiał jest relacją z tej wizyty, w ramach której pokażemy Wam m.in., jak produkuje się moduły pamięci RAM. Zanim jednak przejdziemy do konkretów, najpierw krótkie przedstawienie tego przedsiębiorstwa. Wilk Elektronik na polskim rynku działa od 1991 roku, przez lata będąc dystrybutorem pamięci RAM w naszym kraju. Momentem przełomowym dla tego podmiotu był 2003 rok, kiedy to otwarta została fabryka modułów pamięci i zadebiutowała marka GOODRAM, która jak dobrze wiecie, jest z nami do dnia dzisiejszego, choć z odświeżonym logo w stosunku do pierwowzoru ;) Przez kolejne lata Wilk Elektronik rozszerzał swoją ofertę o kolejne produkty oraz nawiązywał współpracę z firmami z branży półprzewodników, a obecnie w portfolio odnajdziemy w segmencie konsumenckim pamięć RAM, dyski SSD na interfejsach SATA, M.2 i USB, karty pamięci oraz pendrive'y. Ponadto polski producent wytwarza analogiczne urządzenia, ale skierowane na rynek serwerowy i przemysłowy, oraz w wersji reklamowej, do czego jeszcze wrócimy. Za to w temacie konsumenckich pamięci RAM warto jeszcze podkreślić, że w ofercie od jakiegoś czasu są moduły DDR5 o taktowaniu do 6800 MHz.
Jeśli chodzi o samą fabrykę, w 2021 roku rozpoczęła się jej rozbudowa, która została zakończona w 2023 roku. W siedzibie przedsiębiorstwa znajdują się oczywiście liczne pomieszczenia biurowe czy sala konferencyjna, niemniej tym, co nas dzisiaj interesuje, jest oczywiście część produkcyjna, na którą składa się kilka hal, gdzie każda z nich zajmuje się inną częścią procesu wytwarzania produktów. Na zdjęciu niżej zobaczycie według mnie najważniejsze pomieszczenie, ponieważ to właśnie tutaj powstają gotowe moduły pamięci RAM (ale jeszcze bez radiatorów oraz naklejek), które następnie także tu są testowane.
Najważniejsze komponenty potrzebne do wyprodukowania modułu RAM
Zaczynając od składników budulcowych modułów RAM, najważniejsze komponenty to płytki drukowane, które do fabryki docierają w hermetycznych opakowaniach, oraz oczywiście kości pamięci. Podczas wizyty widziałem akurat chipy DDR4 firmy Samsung, niemniej z doświadczenia, bo przecież miałem okazję testować różne produkty marki GOODRAM, mogę powiedzieć, że oprócz produktów koreańskiego przedsiębiorstwa polski producent chętnie sięga też po układy firmy Hynix. W kwestii możliwości technicznych modułów to właśnie kości mają kluczowe znaczenie, gdyż to od nich zależy, jakie taktowanie fabryczne może osiągać pamięć wyprodukowana z ich użyciem, oraz jakie ma możliwości OC. Przykładowo w modułach DDR4 z linii IRDM PRO Crimson White stosowane są chipy Samsung D-die, w zupełności wystarczające przy taktowaniu 36000 MHz, ale rodzina IRDM PRO Hollow White dla wariantu 4000 MHz korzysta z Hynix DJR, z uwagi na znakomitą zdolność tych chipów uzyskiwania wysokich zegarów.
Poszczególne etapy produkcji, czyli jak poskładać pojedyncze elementy w całość
Przechodząc do procesu produkcji, pierwszy etap to nałożenie pasty lutowniczej, co wykonuje specjalna maszyna korzystając przy tym z matrycy, która określa, w których miejscach płytki drukowanej ma być spoiwo lutownicze. Pasta lutownicza znajduje się w niewielkich pojemnikach oraz zgodnie z dyrektywą RoHS, nie zawiera ołowiu. Po zakończeniu jej nakładania, ma miejsce wizualna inspekcja z użyciem techniki laserowej, która określa, czy etap ten zakończył się powodzeniem.
Następnie na tak przygotowaną płytkę drukowaną trzeba nałożyć elementy pasywne, tj. rezystory i kondensatory, oraz aktywne - przede wszystkim kości pamięci. Komponenty pasywne pobierane są z taśm, zaś aktywne z tacek i warto dodać, że taka maszyna firmy Panasonic jest w stanie nałożyć 35 tysięcy elementów na godzinę. Natomiast parametr "Rate", który widać na zdjęciu, określa przez jaki procent czasu maszyna rzeczywiście wykonuje pracę i docelowo ma być oczywiście jak najwyższy, jednak podczas wizyty produkcja została na pewien czas wstrzymana, w związku z czym ma on relatywnie niską wartość - 57,89%. W temacie pamięci DDR5 należy jeszcze nadmienić, że oprócz kości na laminacie montowany jest także układ PMIC, który zasilany jest linią +5 V oraz odpowiada za regulację napięcia na liniach VDD, VDDQ i VPP, które standardowo mają wartość 1,1/1,1/1,8 V. To spora zmiana w stosunku do DDR4, gdzie na płycie głównej zgodnej ze starszym standardem znajduje się osobna sekcja zasilania dla RAM i to ona odpowiada zarządzanie woltażem.
W następnym etapie płyta drukowana z nałożoną pastą lutowniczą i podzespołami elektronicznymi trafia do pieca lutowniczego, który ma ustawioną odpowiednią krzywą temperatury, po czym produkowany moduł jest już niemal gotowy do pracy. Po zakończeniu lutowania ma miejsce druga inspekcja wizualna, która weryfikuje, czy wszystkie elementy są na swoich miejscach. Ale same oględziny, nawet z techniką laserową, nie sprawdzą rzeczy kluczowej, czyli jakości lutowania. Aby zweryfikować ten aspekt, niezbędne jest prześwietlenie rentgenowskie i widok, który chcemy ujrzeć, to czarne pola bez żadnych białych plam w środku (pierwsze ujęcie). Pojawienie się tych ostatnich (jedną z nich zaznaczyłem na drugim zdjęciu) oznacza pęcherze powietrza w spoiwie lutowniczym, co taki moduł niestety dyskwalifikuje.
Po produkcji przychodzi czas na testy weryfikujące sprawność modułu
Potem ma miejsce prosty test elektryczny, który sprawdza, czy w danym module nie ma zwarcia, oraz zapisanie właściwych dla danego modelu danych SPD w układzie EEPROM. Jak nieraz mieliście okazję zobaczyć w naszych testach, w SPD znajduje się całkiem sporo danych, m.in. wytwórca pamięci, oznaczenie modelu, numer seryjny, data i miejsce produkcji, dostawca chipów i ich rewizja oraz profile JEDEC i XMP/EXPO. Moduł, który przeszedł ten etap, można wreszcie przetestować w praktyce, gdzie wykorzystywane są liczne platformy testowe, które de facto są takim samym sprzętem, jaki macie w domach, tyle że ze wzmocnionymi slotami RAM, aby nie było problemów z wytrzymałością płyt głównych. Odnośnie laptopowej pamięci SO-DIMM, jest testowana z użyciem adapterów.
Co do samego procesu testowania, wykorzystywane tutaj oprogramowanie jest autorskie i powstało na podstawie praktycznej obserwacji działania procesorów oraz ich kontrolerów RAM. Testy są tak opracowane, aby do pewnego stopnia symulować typowe codzienne czynności wykonywane na komputerze, ale jednocześnie duży nacisk został położony na jak najskuteczniejsze wykrywanie błędów i badanie stabilności całej dostępnej pojemności modułów. Zestawy RAM składające się z pary modułów są testowane w całości, ponieważ nie ma potrzeby badania modułów osobno, gdyż program w razie wystąpienia błędu jest w stanie wyliczyć fizyczny adres przekłamania, co pozwala określić, który moduł i która konkretnie jego kość jest wadliwa. Cały proces trwa od 20 do 40 minut. Dla pamięci serwerowej testowanie wygląda podobnie, ale z dwiema różnicami. Po pierwsze, program testujący sprawdza, czy nie występują błędy ECC, gdyż sytuacja, że moduł funkcjonuje "poprawnie" tylko dzięki temu, że ECC naprawiło przekłamanie, jest niedopuszczalna. Po drugie, testowanie stabilności odbywa się w podwyższonej temperaturze 80 °C, dzięki specjalnym hot boxom, które precyzyjnie utrzymują warunki termiczne na zadanym poziomie.
Inne ciekawostki związane z wyposażeniem i funkcjonowaniem fabryki
Ciekawym wyposażeniem fabryki jest też komora klimatyczna, służąca do weryfikacji funkcjonowania produktów w nietypowych warunkach temperaturowych. Taki test polega na schłodzeniu do temperatury ujemnej, a później stopniowym jej podnoszeniu do 0 °C oraz powyżej tej wartości. Przy czym, żeby nie było nieścisłości, próba ta nie jest wykonywana dla każdego egzemplarza danej części, który opuszcza linię produkcyjną. Test klimatyczny jest przeprowadzany głównie przy wprowadzaniu produktów w nowej technologii, np. z użyciem innych kości, tak aby sprawdzić, jak świeży model zachowuje się w wymagających warunkach.
Na koniec mamy jeszcze halę, w której odbywa się ostatni etap produkcji - głównie naklejanie etykiet na moduły RAM i montaż radiatorów. Choć nie tylko, gdyż w tej części fabryki ma miejsce również personalizacja produktów, gdzie wskazać można grawerunki na radiatorach (np. na potrzeby producentów gotowych pecetów) oraz nadruki na obudowach pendrive'ów. Przy czym nie jest to jedyna forma personalizacji, bo ta może dodatkowo obejmować sferę techniczną. Przykładowo klient może zażyczyć sobie partię reklamowych pendrive'ów z wgraną prezentacją odnośnie swojej firmy, które mają być widoczne jako CD-ROM, tzn. bez możliwości jej usunięcia. Tudzież możliwe jest bardziej zaawansowane partycjonowanie, gdzie część pamięci USB zawiera wspomnianą prezentację, a reszta jest dostępna do dowolnego użytku.
I tak oto dotarliśmy do końca relacji z wizyty w fabryce Wilk Elektronik. Myślę, że w ramach niniejszego materiału poruszyłem wszystkie najistotniejsze aspekty związane z produkcją modułów pamięci RAM, ale jeżeli macie jakieś pytania, piszcie śmiało w komentarzach, gdyż na wszystkie postaram się odpowiedzieć. A co warto jeszcze dodać, z fabryki zabraliśmy ciekawy upominek widoczny na ostatnim zdjęciu i już teraz mogę uchylić rąbka tajemnicy, że w najbliższym czasie pojawi się osobny materiał poświęcony temu produktowi. Zaglądajcie zatem na ITHardware regularnie, gdyż ciekawych treści nie będzie brakować w nadchodzących tygodniach.
Chcecie zobaczyć relację z wizyty w fabryce Wilk Elektronik z innej perspektywy? Zapraszamy na film na kanale ZMASLO:
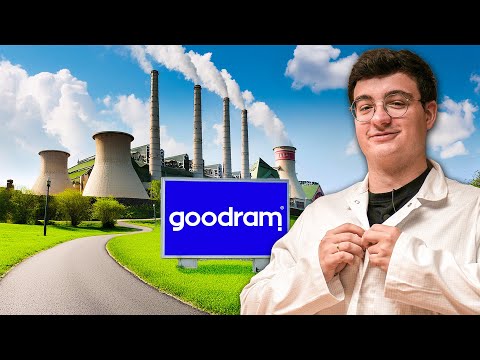

Pokaż / Dodaj komentarze do: Tak produkuje się pamięć RAM. Relacja z wizyty w fabryce Wilk Elektronik